
OVER 50 YEARS OF EXPERTISE AND TRUST
Industrial Furnaces
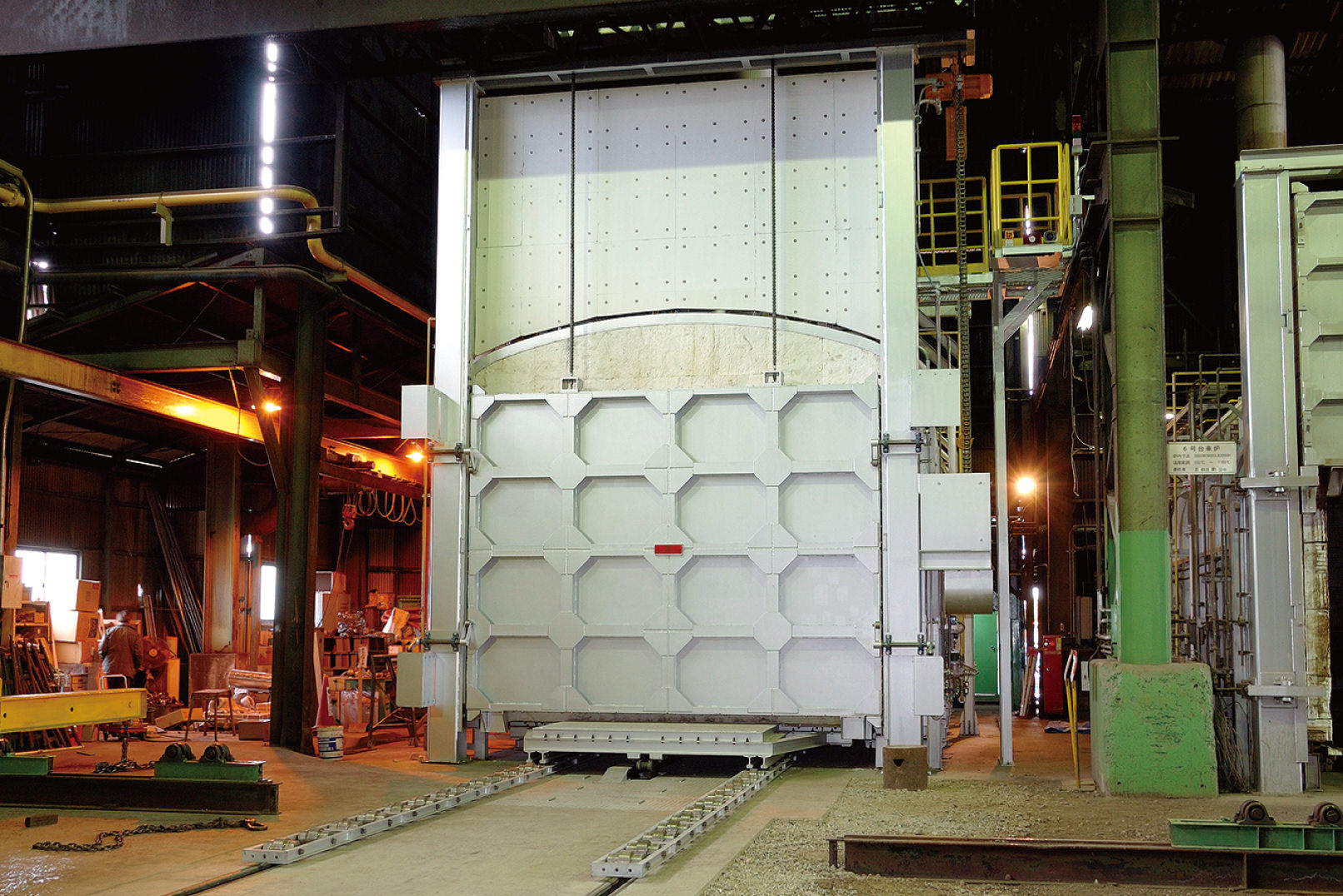
INDUSTRIAL FURNACE
Fully satisfy requirements with advanced technology
Industrial furnaces are our core product.
We respond to customers’ evolving needs with over 50 years of experience, expertise and advanced technology.
The following are our major products. We specialize in made-to-order manufacturing.
Tell us what you need. Products are made to order according to your environment and requirements.
VACUUM FURNACE
We offer made-to-order vacuum furnaces that meet various needs, such as vacuum heating, N2 or Ar gas heating under reduced to normal pressure, and use of process gases.
Vacuum batch furnace
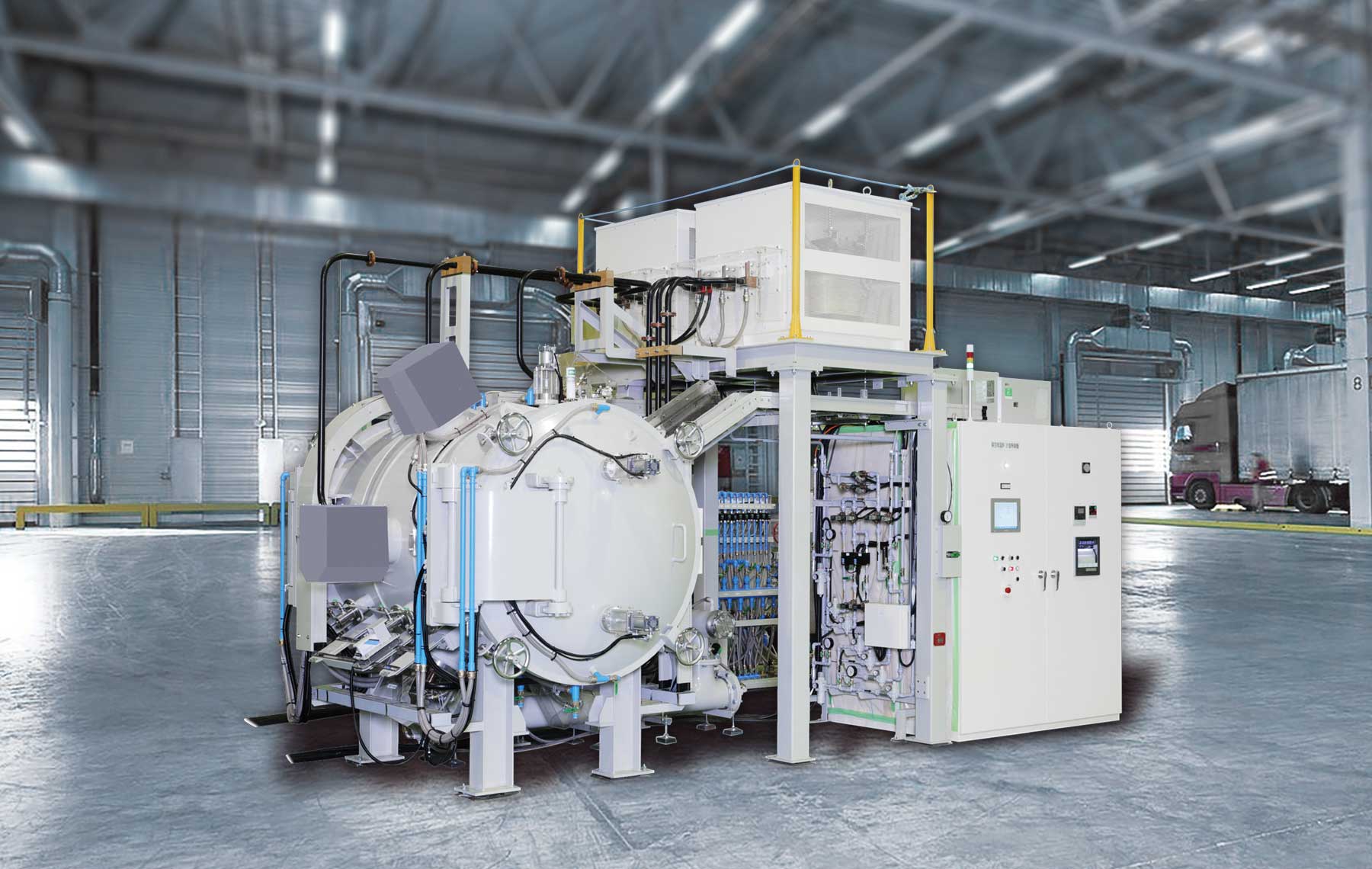
Features
●High vacuum atmosphere
●Temperatures up to 2500°C
●Improved temperature distribution accuracy through two-zone (upper and lower) control inside the furnace
●Shorter cooling time through forced gas cooling and a heat exchanger
Furnace details
The temperature can be raised up to 2000°C for a high vacuum atmosphere and 2500°C for a normal pressure gas atmosphere, allowing various heat treatments even for new materials.
The furnace is separated into upper and lower heating chamber zones, with a graphite heater used for heating and controlling, to improve the accuracy of temperature distribution. Forced external gas cooling and heat exchanger options are available to shorten the cooling time.
Vertical continuous batch treating furnace
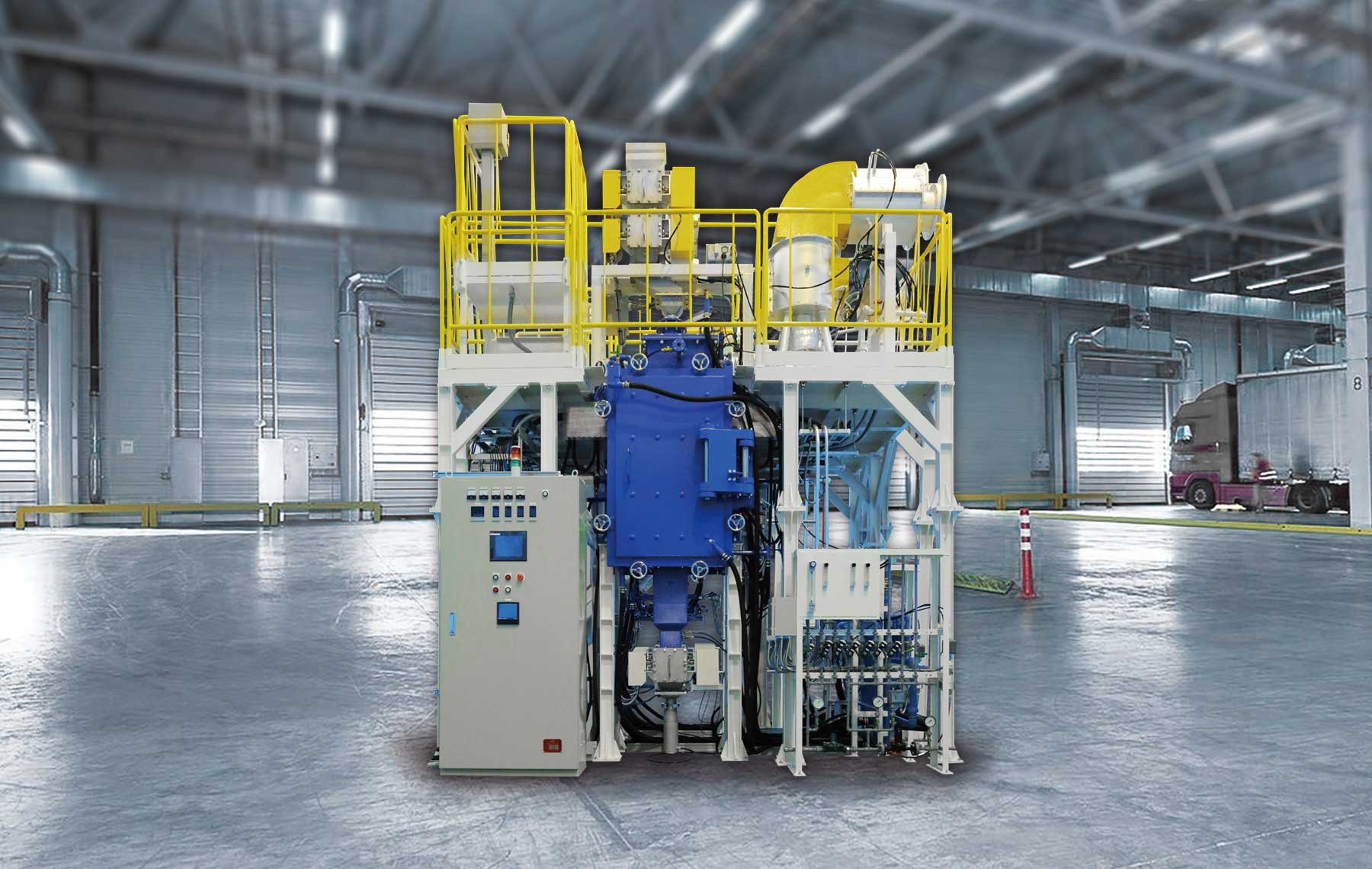
Features
●Vertical furnace designed for continuous batch processing of powders
●High-temperature specifications for ceramics and carbon powders
Furnace details
This vertical furnace allows continuous batch processing without powders being exposed to the atmosphere.
This is feasible even without using a jig such as a tray because product powders are supplied and discharged through a double damper.
Continuous vacuum furnace
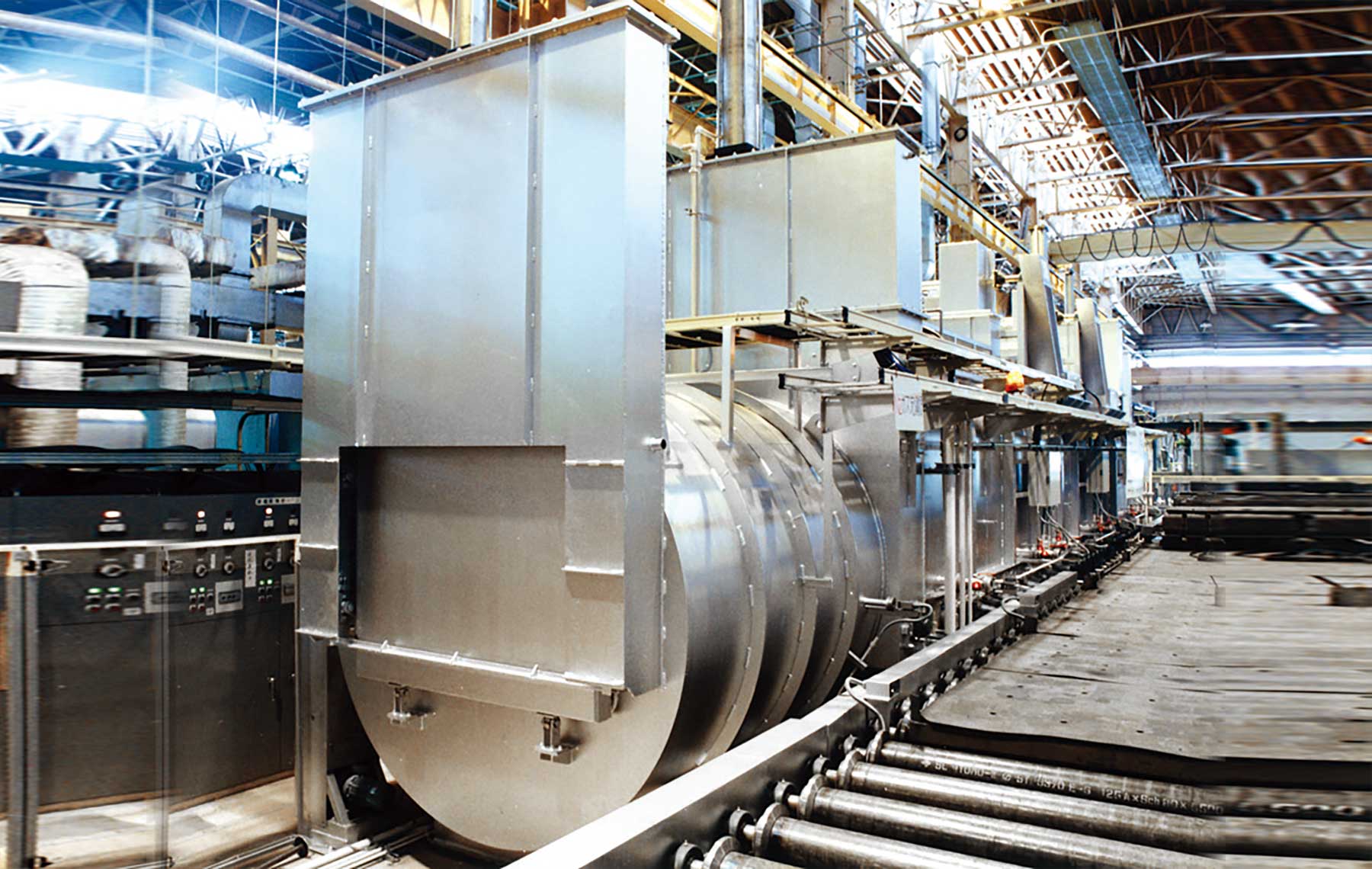
Features
●Continuous production in a non-oxidizing atmosphere
●A wide temperature range supported by a selection of furnace structure materials
Furnace details
With vacuum exchange chambers on the inlet and outlet sides, this furnace enables continuous production in a non-oxidizing atmosphere.
A furnace with high-temperature specifications for 2000°C or higher can also be designed according to the product to be processed.
OTHER LINEUP
Sintering hot press
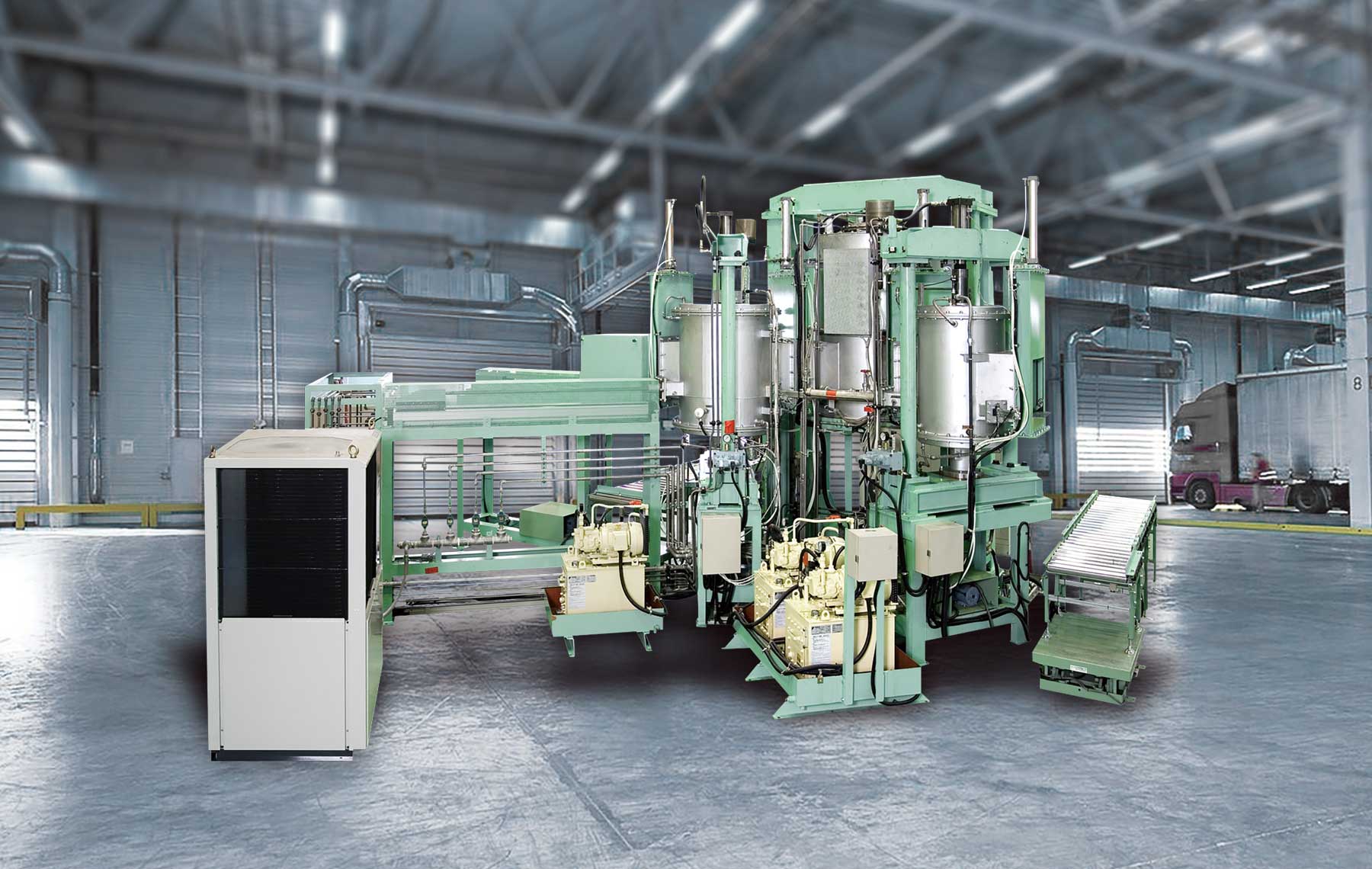
Features
●Pressing mechanism available for each of the heating and cooling chambers
●Temperature and pressure freely programmable
●Unmanned operation possible using full-automatic transfer
●Suitable for high-mix low volume production
●Atmosphere gas (N2 or H2)
Furnace details
A single-chamber batch furnace operates in a cycle of heating and cooling, worsening production and energy efficiency. Meanwhile, a double-pressure hot press has independent heating and cooling chambers, thus greatly reducing the wait time for each process to change its processing conditions. This allows the processing conditions of the next workpiece to be prepared during the preceding workpiece processing. As a result, workpieces with different processing conditions can be switched quickly, which is effective in high-mix low volume production.
Each chamber is equipped with a hydraulic pressing mechanism to minimize thermal expansion in each process of heating and cooling. The atmosphere in each chamber purges N2 or H2 gas to prevent workpieces from being oxidized, along with high sealing performance throughout the equipment.
High-purity annealing furnace for quartz glass parts
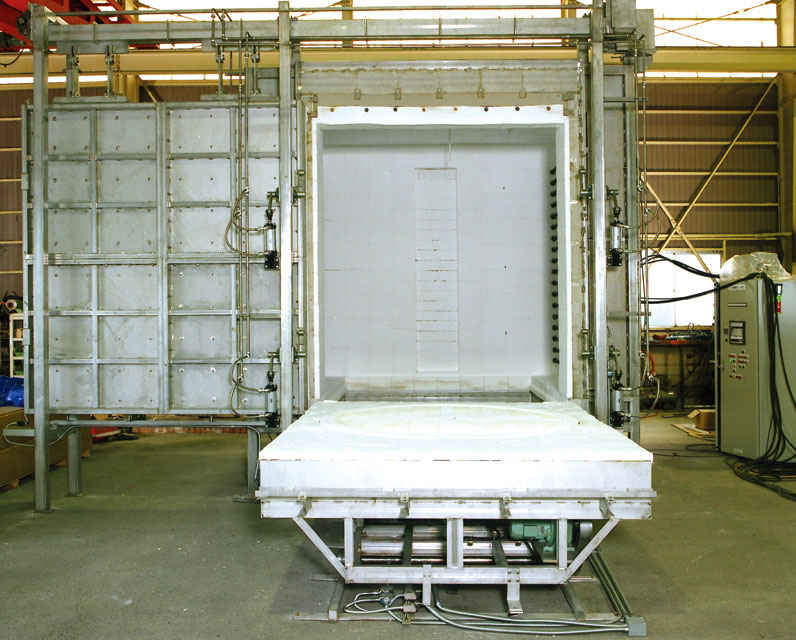
Features
●Stainless-steel furnace body and high-purity insulation for high cleanliness
●SiC heater used as a heat source to improve the temperature distribution
●Can be tailored according to target product size
Furnace details
Annealing furnaces for quartz glass products used in the production of electronic components or semiconductors require high cleanliness with minimal contamination. Our high-purity annealing furnace for quartz glass parts uses high-purity ceramic fiber with reduced impurities as lining insulation and the furnace body is made entirely of stainless steel, thus greatly reducing contamination on the surfaces of quartz glass products in the annealing process.
To process larger or longer products, we are working on making larger furnaces to meet customer demands.
Hot air stirring type continuous heat-treating furnace
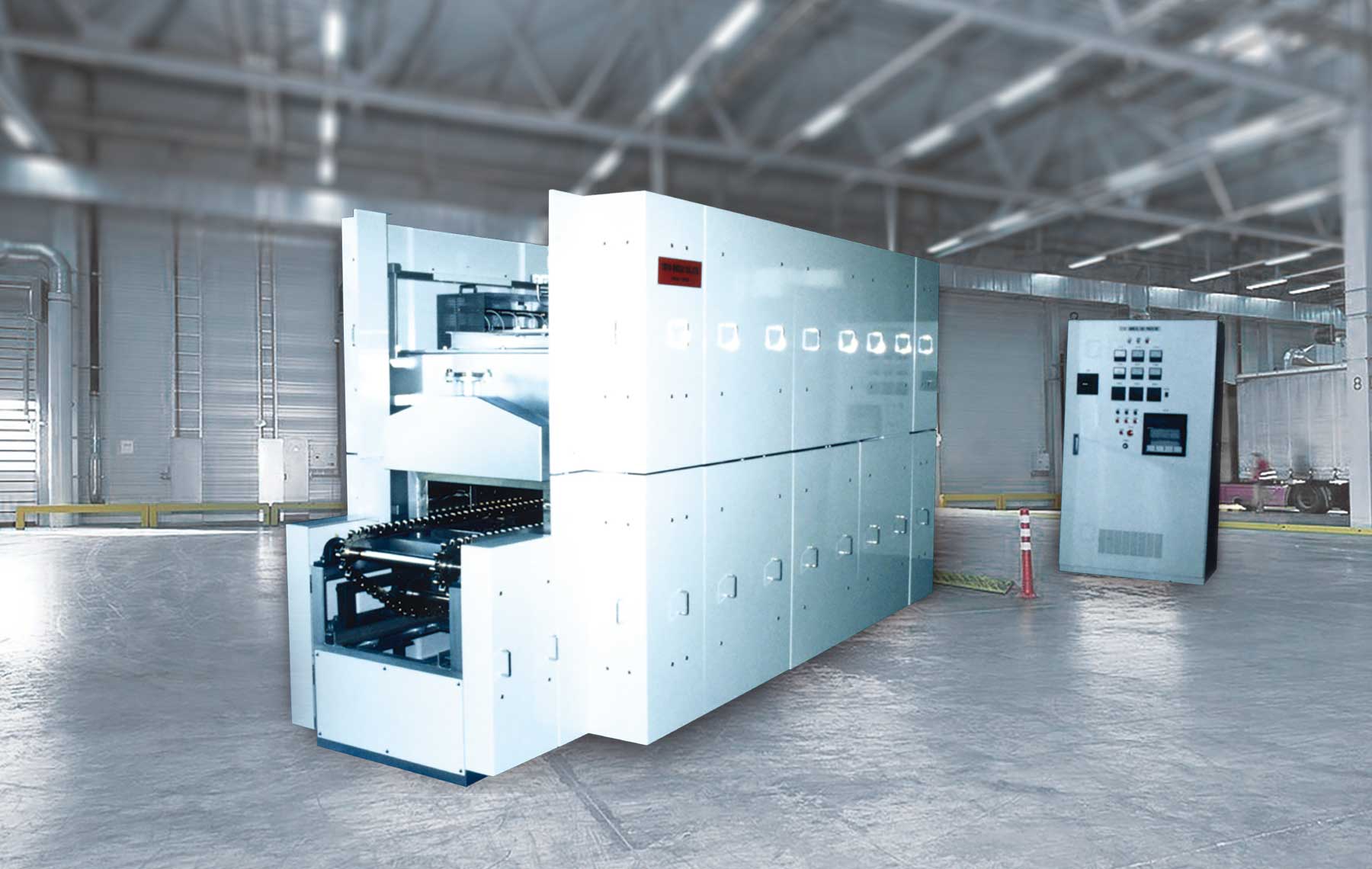
Features
●High temperature distribution accuracy
●Insulation covered by stainless steel thin plates to reduce furnace contamination
●Selection of transfer method to suit the product to be processed
Furnace details
This furnace stirs the hot air evenly using a furnace fan, achieving a temperature accuracy of ±2°C in an effective area even in a relatively low temperature range between 200 and 400°C.
A walking beam transfer system is adopted for products that require cleanliness to minimize contamination generated from the driving and sliding parts.